Hi community,
I'm hoping someone might be able to help me clarify this issue.
I have an Poduction order item (Item A) which has a multi-level bom, and one of the component is also a production item with a bom (Item B)
The item setup is as following
|
Item A |
Item B |
Replenishment system |
Production Order |
Production order |
Manufacturing policy |
Make-to-order |
Make-to-order |
Re-order policy |
Lot-for-lot |
Order |
When I create a production order for Item A and refresh, because Item B is make-to order, it inserted a second production order line item like below.
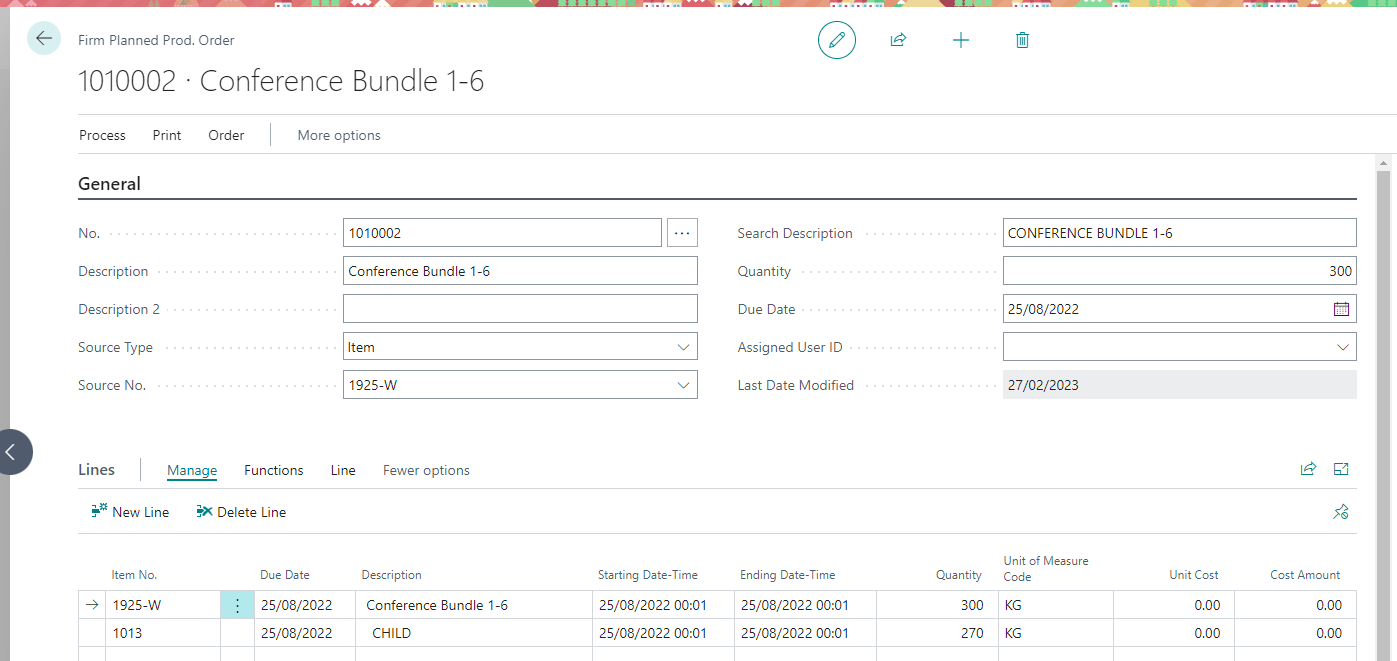
But if I run MPS, and then carry out action to create a production order for Item A, it only creates a production order created will only have the parent item (Item A) in production order line
The item B will only be picked up if I run MRP after (or together with MPS) - regardless of manufacturing policy.
But if I refresh the production order that was created by MPS for Item A, then the second line for Item B will appear in the order line again.
My expected outcome was that when an order created for Item A with MPS, it will still create a second line if the Item B is set to made-to order.
But if it's set to made to stock, then it will prompt on MRP to create an order to replenish Item B.
Could someone please help me clarify if my expected outcome is what everyone else thinks it should be behaving, or how it's currently behaving is correct?
Struggling to identify whether this is a bug or a standard feature.